Our Products:
Contact Sourcefy:
Address:#108-209 Glen Cove Rd
Carle Place, NY
United States 11514
Email: support@sourcefy.com
Toll-free: 1-855-585-4430
Map
Articles
Forklift Training - Basic Operations
Posted on
Whatever type or brand, the industrial forklifts used in many domains have been instrumental in lifting and transporting heavy materials to different points of locations. It’s hard to imagine warehouses, retail stores, department stores, and even grocery shops without the employment of these forklift machines.
The benefits that these forklifts bring to the table have even grown to impressive proportions mainly for the way they have been developed over the years from technological advancements.
However, there’s one big issue in the acquisition and maintenance of these industrial forklifts: the basic knowledge of how they can be operated. Not only is it important for these operators to have a basic instruction of these machines’ operation procedures, but an operation manual should be made available.
Even if there may already be hundreds of brands of lift trucks that run a variety of everyday operations, an outline of how these forklifts are operated could go a long way to improving productivity. This article will attempt to offer such a general outline of a forklift’s manual.
Step-by-Step Guide To Operating A Forklift
1. Getting on/off and starting
The first step is for the operator to make sure that the forklift is in a proper safe position in relation to the pallet or load board to be transported. A good estimate for this would be to allocate about ½ to ¾ of the pallet width to position the forks and make them symmetrical to the forklift. After approaching the pallet, the operator must press the brake paddle to halt at 20 to 30 cm before shifting it into neutral.
The operator should next inspect whether the front and rear of the forklift are in sync before mounting the forklift seat from its left, with the operator’s left hand holding on the assist grip. It’s important for the operator to remember to only ever use the left side of the forklift to get on and off.
The next step would be to make sure that the rear mirrors have no deterrence or any form of interference. Operators should be reminded, too, that adjusting these mirrors are only permitted when the vehicle is still immobile or stationary and that they never grab the operation levels, including the steering wheel, when the forklift is already mobile. It’s extremely prohibited, too, to jump off/on a forklift when it’s already moving.
The next step would be to pull the steering knob using the operator’s left hand, and then confirm that the level is already in neutral position and that the parking brake has already been set. Then, the key may now already be inserted in the ignition and the engine started.
The forks must be lifted to about 5 to 10 cm from the ground, before tilting the mass fully backward. After this, the break paddle must be depressed before starting to move the forklift. Of course, you should inspect the surroundings first before shifting select into reverse and releasing the parking brake for safety.
When the safety is confirmed, the break paddle must be depressed and then shift the select lever into a forward position. The next part is to release the parking brake and press the accelerator paddle to move forward.
2. Right-angle maneuver (forward and reverse positions)
The next area to check is the right angle turns to know if the forklift can drive forward to the center while also being able to reach corners without restrictions. After this stage, the operator is able to check the forklift parking brake release, directional lever and whether the back-up siren works properly.
For right angle turns, the first thing for operators to remember would be to drive forward to the center of the aisle and approach the corner gradually. It’s only when the backrest of the forklift has reached the corner that the operator can start turning.
Right immediately after the middle section arrives at the center of the aisle, the operator may now return to straight position. To do a right angle turn, the operator needs to first drive the forklift backward to the center of the aisle.
When the front wheels are already at least 1 meter from the corner, the operator can already confirm the corner to turn. It’s important to remember to always turn quickly at the exact time when the forklift front wheels would pass the corner. Afterwards, return to a straight position quickly while checking both the center of the counter weight as well as the aisle’s center behind.
During the forklift’s right angle reverse turns, the operator must first observe if the load is blocking their vision. If it does, the operator can just keep driving backwards and adhere to the forklift’s turning ability while driving slowly and being always aware at the same time.
To ascend the forklift, the driver has to position the load uphill. Never drive askey or attempt to suddenly make direction changes in the middle of the slope. If the height of the load is higher than the driver’s backrest, the cargo must be secured that it won’t fall over.
3. Loading
To make loading adjustments, the operator should first approach and square up to the pallet stand before stopping at 20 to 30 cm away from it to depress the brake paddle. Then, you should then apply the parking brake and shift select into neutral. The next step would have to require the operator to position the mast into a vertical position, lift the forks to the level of the pallet opening’s height before inspecting the surroundings for safety.
When the forklift’s brake pedal is being depressed, the select lever should be shifted into forward. The parking breaks can in this part be already released. To prevent rollover accidents, operators should ensure that the load is secure, balanced and stable, and should only handle the loads within the forklift’s capacity. No one should also be allowed to stay onto the pallet and underneath it during lifting.
The next step is to move forward slowly before inserting the forks completely into the pallet. When this is settled, it’s time to depress the brake to a complete halt. The next part would be to apply the parking brake before shifting the select into neutral. Afterwards, the pallet must be lifted 10 cm above the pallet stand.
Next, the select level must be shifted into reverse and then the parking brake released. The forklift should then be moved backwards and only be stopped when the pallet is already 20 to 30 cm away from the pallet stand. Then, apply the parking brake, shift the select into natural, and then lower the forks slowly to about 5 to 10 cm above the ground. When these parts are now stable, the operator can now tilt the mass fully backward. The last part in this stage would be to shift select into reverse before finally releasing the parking brake.
During all this, the surroundings must be checked for safety issues before moving. Operators must also check the surroundings are clear from hindrances and physical barriers, especially in the front and on the sides where there’s often a blindspot. They should also release the parking brake and press the accelerator paddles by moving forward to see whether there are any defects.
4. Unloading
The first step to unloading would be to approach and square up to the pallet stand. Then, the operator must stop 20 to 30 cm away from it by depressing the brake paddle. The parking brake must then be applied and the shift select be put into neutral.
Afterwards, it’s time to position the mast to a vertical position before lifting the pallet around 15 cm above the pallet stand.
Then, the select lever must be shifted forward before finally releasing the parking brake. The next part would be to move the forklift forward slowly until the pallet is placed directly above the unloading position. This is now the time to depress the brake paddle to a stop, then apply the parking brake and, finally, shifting the select lever into neutral.
The operator has to also make sure during this stage that the lift, right and forward area are inspected to ensure that it’s safe to proceed. After this, the select lever must be shifted into reverse and then the parking brake released. Then, the forklift should be moved backwards until the forks are about 20 to 30 cm away from the pallet.
The parking brake then would have to be applied, and the lever shifted into neutral, before lowering the forks to about 5 to 10 cm above the ground. Next, the mast must be tilted to full backward position. After doing this, the operator can now lower the forks to the ground to set the load in place, ensuring that the forklift’s hydraulic system is given no unnecessary pressure.
5. Parking, turning off the machine
Turning off the machine should start by depressing the brake paddle, then stopping the forklift on level ground, before applying the parking brake and shifting it into neutral to make sure that the operator can get off the forklift safely. The forks have to also be lowered to until 70% of the tips of the forks are already touching the ground.
When it’s done, it’s now good to turn the key ignition off and remove the key. The operator can now get off the forklift by placing their left hand on the assist grip first and their right on the backseat. It’s important to remember that abrupt acceleration, abrupt braking and abrupt turning, as well as tilting the forks forward or backward when they’re loaded and raised, can cause serious accidents.
Extra Tips:
- The first thing to remember before operating a forklift is going through a checklist that enlists the safety cautions, the areas that have to be inspected, among others. If the forklift operated fails to pass the checklist, it’s helpful to tag it for out-of-service.
- The operator should also at all times never forget to protect his hand from being entangled into the forklift itself.
- Accidents are easily avoided when the forklift operator checks for pedestrians and hazards as the forklift is run. Honking is a simple but effective way to ensure accidents won’t happen, considering the forklifts sit somehow lower than an average pedestrian’s view.
- The operator should adjust the forks using all of the levers, which are the left, middle and right. It’s advisable to move slowly around while lifting the load, as well as putting the forklift in neutral mode and set the parking brake when immobile. It’s important to see, too, that the load to be transported is positioned in the center of the forks and balanced.
- To check the lifting capacity of the forklift, the operator should lift the load through pulling the leftmost lever towards the operator. Keeping the load low is advisable, almost leveled to the ground, to make sure that the forklift’s center of gravity is at its most stable.

Forklift Masts - different types and what they're suitable for.
Forklift operators have at all times to examine and distinguish the different types or classifications of forklift masts. For starters, these masts are what is commonly known as an “upright” and are to be the vertical assembly installed at the front of the forklift. This mast is responsible not just for the raising, lowering and [...]

Aftermarket vs OEM
Aftermarket vs OEM Parts When the time comes to make a repair on your vehicle, look into using aftermarket parts instead of parts sourced directly from the manufacturer (OEM). There are a number of benefits of using aftermarket parts on your vehicle. Lower Cost Aftermarket car parts are generally much more affordable compared to OEM parts. Part [...]

What's a Pallet Jack?
A pallet jack or jacks are also known as pallet trucks, pallet pump, pump truck or jigger. All those names refer to a tool that is used to lift and move pallets. We can also define them as manually operated device for lifting and moving pallets. Pallet jacks are the most basic type or form of a forklift. Their main [...]

Doosan Daewoo Forklifts
Doosan Industrial Vehicle America Corporation (DIVAC) is based in Buford, Georgia. Its headquarters spread on over 170,000 square foot facility. The headquarters is also the home of parts operations that are currently supplying over 25,000 line items to its affiliate groups. Doosan Industrial Vehicle group supplies material handling equipment to the US market through more than 80 independent dealer companies. Their dealers [...]

Genie Aerial Lift parts
Genie Aerial lifts is an American corporation that manufactures aerial work platforms. It is owned by Terex Corporation now, also an American Corporation, a leading aerial lift and material handling manufacturer based in Westport, CT, United States. Genie was formed by Bud Bushnell in 1966 and was an independent company until 2002 until Terex corporation acquired it. Headquarters are currently [...]

Komatsu Forklift Parts
Komatsu Ltd. Or just Komatsu is a Japanese corporation that in its product line has construction, military and mining equipment. Besides those company also produces thermo-electric generators, lasers, press machines, military equipment and other kind of specialized equipment. The corporation was named after the city where it was founded, Komatsu, Ishikawa. Ko matsu on Japanese also means small pine three. When [...]

TCM Forklift Parts
It was back in 1949 when Toyo Carriers Manufacturing Co., Ltd., the predecessor of UniCarriers Corporation, manufactured the first internal combustion engine forklift truck made in Japan. That first forklift had almost the same features as the forklifts we see today. Those features are hydraulic system for lifting and lowering, rear steering and lifting lever positioned on the right side [...]
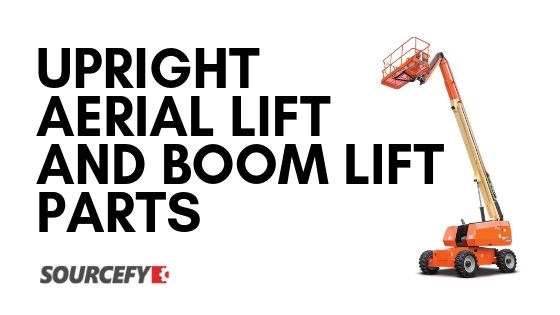
Upright Aerial Lift and Boom Lift Parts
Upright Aerial lift is also known as Aerial device, and aerial work platform (AWP) or even Mobile Elevating System (MEWP). No matter what name is used, its main purpose stays the same: It is a device used to provide access for people and equipment at different areas, usually at height. Its flexible and long access reach differentiates them from [...]
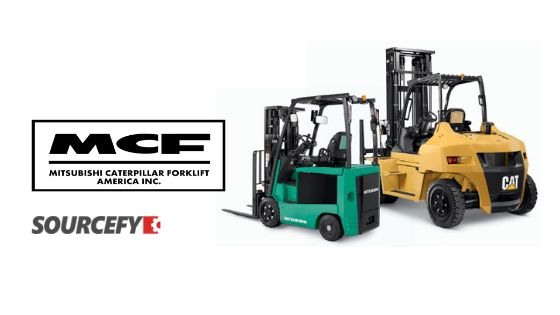
Mitsubishi and Caterpillar Forklift Parts
Mitsubishi Caterpillar Forklift America Inc. ("MCFA") is based in Houston, Texas. MCFA was formed through a joint venture between two major companies, Mitsubishi Heavy Industries, Ltd. (MHI) and Caterpillar Industrial Inc. (CII). Jungheinrich Forklifts joined this partnership through a manufacturing and distribution agreement with MCFA. Mitsubishi Caterpillar Forklift America manufactures and distributes material handling equipment and spare parts under the Mitsubishi Forklift Trucks, [...]